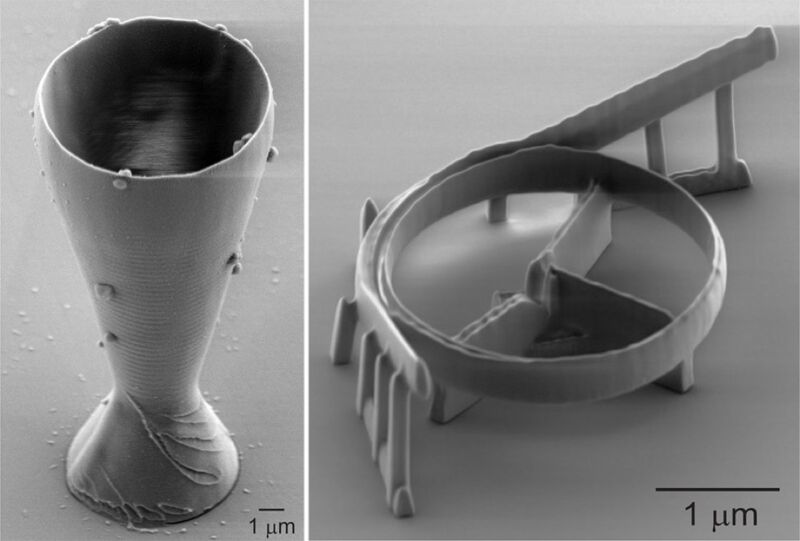
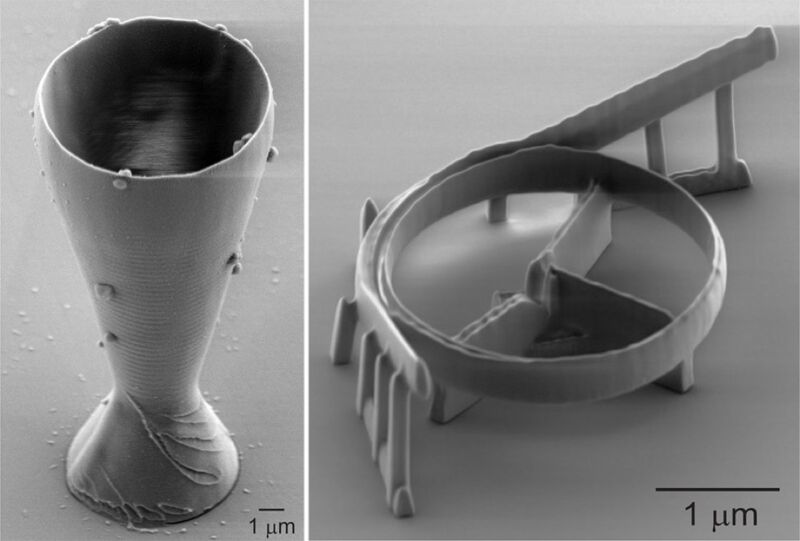
KTH Koninklijk Instituut voor Technologie
Een team van Zweedse wetenschappers heeft een nieuwe technologie voor 3D-printen ontwikkeld Silica glas Vereenvoudigt complexe energie-intensieve processen. Als proof of concept printten ze ’s werelds kleinste wijnglas (gemaakt van echt glas) met een frame kleiner dan de breedte van een enkele haar, evenals een optische resonator voor glasvezelcommunicatiesystemen – een van de vele mogelijke toepassingen voor 3D-geprinte componenten van silicaglas. Ze beschreven hun nieuwe werkwijze in Het laatste papier In Natuurcommunicatie.
“De ruggengraat van internet is gebaseerd op optische vezels die van glas zijn gemaakt,” zei co-auteur Christine Gilvason van KTH Royal Institute of Technology in Stockholm. “In deze systemen zijn allerlei filters en vergelijkers nodig die nu met onze technologie 3D geprint kunnen worden. Dat opent veel nieuwe mogelijkheden.”
Silicaglas (d.w.z. amorf siliciumdioxide) is een materiaal dat volgens de auteurs een uitdaging blijft voor 3D-printen, vooral op microscopisch niveau, hoewel verschillende benaderingen proberen deze uitdaging aan te gaan, waaronder lithografie en inkten. . Zelfs die waren slechts in staat om kenmerkgroottes in de orde van grootte van enkele tientallen micrometers te bereiken, met één uitzondering Studie 2021 dat gerapporteerde nauwkeurigheid op nanoschaal.
Maar die worden allemaal gebruikt Sol-gel Processen met verschillende organische mengsels geladen met nanodeeltjes van siliciumdioxide. De uiteindelijke gedrukte structuren zijn daarom composieten die veel organische materialen bevatten en missen dus de meest wenselijke eigenschappen van silicaglas (d.w.z. thermische en chemische stabiliteit, hardheid en optische transparantie over een breed scala aan golflengten). Het vereist een extra sinterstap bij hoge temperaturen van ongeveer 1.200 ° C (2.192 ° F) gedurende enkele uren om de organische resten te verwijderen en die eigenschappen te bereiken. Deze extra energie-intensieve stap beperkt potentiële toepassingen ernstig, aangezien alleen substraatmaterialen kunnen worden gebruikt die bestand zijn tegen hogere temperaturen. Sommige benaderingen vereisen ook dat 3D-geprinte structuren worden geassembleerd tot een definitieve vorm, wat een uitdaging is op micrometerschaal.
Bij het ontwikkelen van hun alternatieve 3D-printtechnologie voor silicaglas, Gylfason et al. Worden waterstof silsesquioxaan (HSQ), een anorganisch silica-achtig materiaal dat kan worden gevormd door elektronenstralen, ionenstralen en bepaalde golflengten van ultraviolet licht. Een groot voordeel is dat hun methode niet afhankelijk is van organische verbindingen die fungeren als fotosensitizers of bindmiddelen die op het substraat achterblijven, zoals het geval is bij lithografie of schrijven met directe inkt. In plaats daarvan berust hun methode op directe verknoping van anorganische HSQ’s.
Het proces heeft drie hoofdstappen. Eerst lieten ze HSQ opgelost in organische oplosmiddelen op een substraat vallen. Zodra de HSQ droog is, traceren ze de gewenste 3D-vorm met behulp van een gefocuste sub-picoseconde laserstraal. Ten slotte wordt elke onbedekte HSQ opgelost met een gewoon gebruik van kaliumhydroxide-oplossing. Raman-spectroscopie van de afgedrukte microstructuren toonde alle verwachte kenmerken van silicaglas.
Er waren echter ook restsporen van waterstof en koolstof. Voor toepassingen die meer zuiver silicaglas vereisen, kunnen resterende organische stoffen worden verwijderd door de structuren te gloeien bij 900 ° C (1652 ° F) – een extra stap toegestaan, maar bij een veel lagere temperatuur dan de gebruikelijke extra sinterstap. Vervolgens werd het spectrum van de structuren afgestemd op een commercieel gefuseerd silicaglassubstraat. Terwijl het uitgloeien van de 3D-microstructuren ervoor kan zorgen dat ze krimpen of vervormen, ontdekten de auteurs dat de maximale krimp voor hun silicaglasstructuren ongeveer 6 procent was, vergeleken met tussen de 16 procent en 56 procent voor glazen objecten gemaakt met behulp van lithografie en directe inktmethoden. . . .
Naast een klein proof-of-concept wijnglas en optische resonator, hebben de auteurs een kleine versie van het KTH-logo, een cantilever en een conische spiraal bedrukt, evenals een optische tip van silicaglasvezel. Ze denken dat hun methode ook kan worden gebruikt om op maat gemaakte lenzen te maken voor medische apparaten en microrobots. Het coaten van 3D-geprinte microstructuren met nanodiamanten of ferro-nanodeeltjes kan verdere aanpassing van de integratie-eigenschappen van hybride kwantumfotonica mogelijk maken of de controle over de beweging van de structuren magnetisch verwijderen.
“De zorgen bij het integreren van 3D-printmethoden zijn meestal verschillend voor verschillende toepassingen,” zei co-auteur Bo Han Huang, een afgestudeerde student aan KTH. “Hoewel optimalisatie van onze methode voor verschillende toepassingen nog steeds vereist is, geloven we dat onze methode een belangrijke en noodzakelijke doorbraak biedt voor 3D-printen op glas voor gebruik in praktische scenario’s.”
DOI: Natuurcommunicatie, 2023. 10.1038 / s41467-023-38996-3 (over DOI’s).
“Social media fanaat. Fanatieke bacon fanaat. Wannabe popcultuur fan. Communicator. Gecertificeerd schrijver.”
More Stories
Wanneer zullen de astronauten lanceren?
Volgens fossielen werd een prehistorische zeekoe opgegeten door een krokodil en een haai
De Federal Aviation Administration schort vluchten van SpaceX op nadat een vlammende raket tijdens de landing neerstort